The origins of Sysplast GmbH go back to the 1970s. At a time when recycling had hardly entered people’s minds, our company’s predecessor began as part of Grundig AG, with the processing of scrap materials from production. By the early 1980s, we had grown to become the Zentrum für Kreislaufwirtschaft (Recycling Management Centre). From 1990, with support from the German Federal Ministry of Education and Research, we developed standards for the recycling of electrical devices which still serve as a guide to other organisations worldwide. Our driving ambition – that resources should be conserved in maximum quantity and quality – is also more alive than ever. Today, as Sysplast GmbH and a member of the energenta group of companies, we stand for the entire value chain of a closed-loop economy that helps not only our customers, but our planet as well.
Your Sysplast team: experienced, flexible and open to developing and implementing your individual solution and accompanying it into the future at a high standard of quality. With a clear ambition: Nothing gets lost.
Sysplast Executive Management:
Udo Dobberke
Phone: +49 (0) 911 / 21 79 38 – 0
Fax: +49 (0) 911 / 21 79 38 – 29
Email: udo.dobberke@sysplast.de
Gisbert Schulte-Bücker
Phone: +49 (0) 911 / 21 79 38 – 0
Fax: +49 (0) 911 / 21 79 38 – 29
Email: gsb@energenta.de
Your contact partners for Purchasing and Sales:
Sven Wächter
Phone: +49 (0) 911 / 21 79 38 – 13
Fax: +49 (0) 911 / 21 79 38 – 29
Email: info@sysplast.de
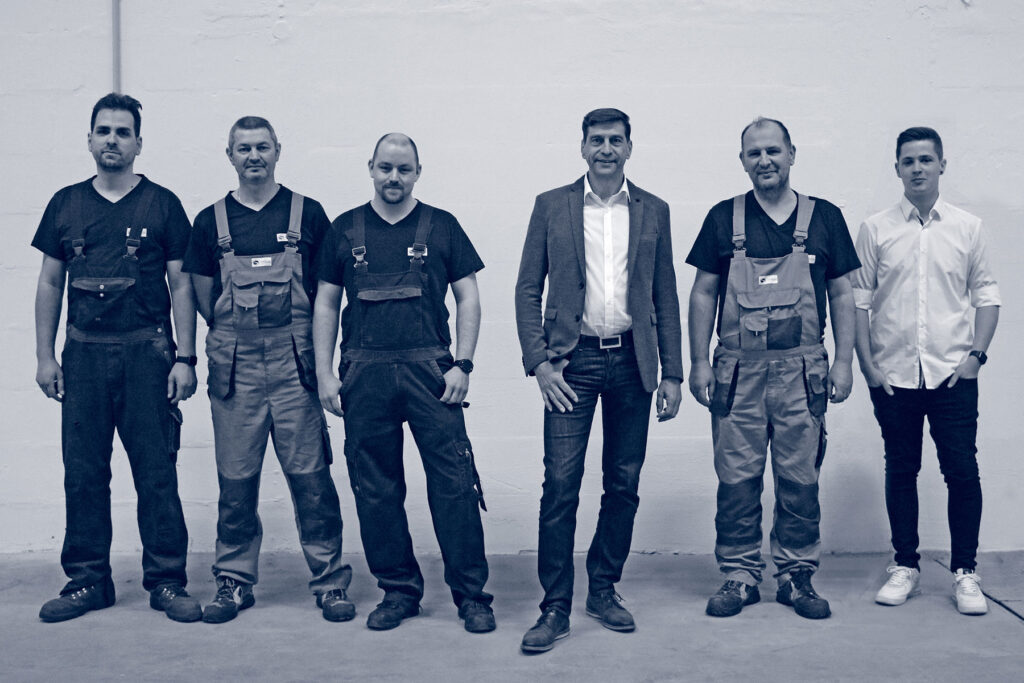
We implement your individual solution in maximum quality
From left to right: Antonio Martin-Lopez (Mixer/Mills), Michael Hansko (Shift Foreman), Jochen Oelker (Production Manager), Udo Dobberke (Managing Director), Lulzim Dulazeka (Shift Foreman), Sven Wächter (Purchasing/Sales)
We have our strong foundation in industry, therefore we understand your special demands.
Chances are, you have encountered Sysplast regranulates and compounds in diverse products – from telecommunication devices to OEM-made auto components. We understand your product quality requirements as a manufacturing enterprise. We listen, respond to your ideas and point out ways in which we can implement or optimise your product cycles, from disposal and processing, to returning reclaimed materials to production. And if there is a particular idea that you seek to realise: formulate your aim, and we will find the solution.
Industries that trust in our quality:
Automotive
Electrical & electronic goods
Packaging
Furniture
Plastics processing
Construction
Telecommuni-cations
Entertainment